Choosing the right rebar tie wire is crucial for the quality of construction projects. Rebar tie wire is mainly used to secure rebar in place, ensuring the structural integrity of buildings. However, different types, specifications,
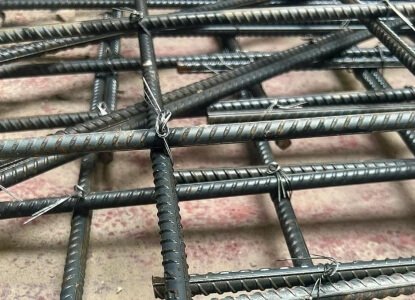
and materials of tie wire are suited for different construction needs. This article will help you understand how to choose the most suitable rebar tie wire based on various project requirements, budget, and environmental conditions, ensuring that your construction projects are efficient and safe.
The choice of rebar tie wire directly impacts construction efficiency and structural safety. This article provides key factors to consider, such as material, specification, corrosion resistance, and tying strength, to help you make an informed choice. Whether it’s a large-scale construction project or a small renovation, choosing the right rebar tie wire can significantly improve project quality and cost-effectiveness. Read on for practical tips on selecting the right tie wire to enhance your project management.
In the construction industry, rebar tie wire is widely used for securing rebar in various structural projects. With the increasing requirements of construction projects, many different types and materials of tie wire have entered the market. With so many options available, how do you choose the right product for your specific project? In the following sections, we will analyze the key factors influencing the choice of rebar tie wire and provide you with effective buying advice.
Table of Contents
Product Name | Material | Specifications | Suitable Applications | Key Features |
---|---|---|---|---|
Hot-Dipped Galvanized Tie Wire | Galvanized | 0.8mm – 1.2mm | Large-scale construction, bridges, roads | Excellent corrosion resistance, ideal for humid environments |
Regular Steel Tie Wire | Plain Steel | 0.7mm – 1.0mm | Small projects, repairs | Cost-effective, suitable for indoor environments |
High-Strength Steel Tie Wire | Alloy Steel | 1.0mm – 1.5mm | High-strength structures, seismic projects | High tensile strength, good earthquake resistance |
Stainless Steel Tie Wire | Stainless Steel | 1.2mm – 1.5mm | Coastal areas, chemical plants, corrosive environments | Exceptional corrosion resistance, suitable for harsh environments |
How To Choose the Right Rebar Tie Wire Material?
Selecting the right material for rebar tie wire is crucial for ensuring the strength, durability, and efficiency of your construction projects. The material of the tie wire determines its performance, longevity, and suitability for various environmental conditions. Below, we will explore the two most commonly used materials for rebar tie wire: galvanized steel and plain steel, as well as their respective advantages and ideal applications.
1. Hot-Dipped Galvanized Tie Wire
Hot-dipped galvanized tie wire is one of the most popular choices due to its excellent corrosion resistance. The wire is coated with a layer of zinc, which protects it from rust and degradation, making it highly suitable for use in moist or corrosive environments.
-
Advantages:
- Corrosion Resistance: The zinc coating provides a protective barrier, preventing rust and corrosion, even in highly humid or wet conditions.
- Longer Durability: The protective layer extends the lifespan of the tie wire, making it suitable for outdoor projects and construction in coastal areas or chemical environments.
- Strength and Flexibility: Galvanized tie wire maintains good tensile strength while being flexible enough for easy handling and installation.
- Rust-Proof: Ideal for environments where rusting would undermine the structure, such as in bridges, roads, and large-scale infrastructure projects.
-
Applications:
- Large-scale construction projects (e.g., bridges, highways, tunnels)
- Areas with high humidity or exposed to moisture (e.g., coastal regions, chemical plants)
- Environments prone to rusting or corrosion
2. Plain Steel Tie Wire (Non-Galvanized)
Plain steel tie wire, or non-galvanized steel wire, is commonly used in standard construction projects where corrosion resistance is not a significant concern. It is often less expensive than galvanized wire and is suitable for indoor or temporary applications.
-
Advantages:
- Cost-Effective: Plain steel tie wire is usually more affordable compared to galvanized wire, making it ideal for smaller projects or when cost is a key consideration.
- Strong and Durable: Although it lacks corrosion protection, plain steel wire is still very strong and durable, especially when used in indoor or dry environments.
- Easy to Work With: It is relatively easy to bend, twist, and cut, making it simple to handle and use during the construction process.
-
Applications:
- Indoor construction projects (e.g., residential buildings, commercial spaces)
- Short-term or low-budget projects
- Temporary structures where corrosion is not a concern
3. Stainless Steel Tie Wire
Stainless steel tie wire is another high-performance option that offers superior corrosion resistance compared to galvanized wire. It is highly durable and is often used in extreme conditions where maximum resistance to corrosion is required.
-
Advantages:
- Superior Corrosion Resistance: Stainless steel is highly resistant to rust and corrosion, even in aggressive environments like marine areas or chemical plants.
- Longevity: It lasts much longer than galvanized wire or plain steel, particularly in highly corrosive environments.
- High Strength: Stainless steel tie wire offers excellent tensile strength, making it ideal for heavy-duty construction applications.
-
Applications:
- Harsh environments with high exposure to chemicals, salt, or extreme temperatures (e.g., chemical factories, coastal regions)
- Long-term, high-value construction projects that require top durability (e.g., bridges, skyscrapers)
- Projects requiring maximum reliability and safety standards
Choosing the right rebar tie wire material depends largely on the specific needs of your project. Galvanized tie wire is ideal for environments with high moisture or exposure to corrosion, while plain steel wire is best suited for budget-friendly, indoor projects. Stainless steel tie wire offers the highest corrosion resistance and is perfect for harsh conditions. By understanding the strengths and applications of each material, you can select the tie wire that will best meet the demands of your construction project.
Rebar Tie Wire Specifications and Sizes
When choosing rebar tie wire, it’s crucial to understand the various specifications and sizes available to ensure the wire is suitable for your construction project. The right specification and size can significantly impact the efficiency of the rebar tying process, the safety of the structure, and overall project costs. In this section, we’ll explore the different specifications and sizes of rebar tie wire, and help you choose the correct one for your needs.
1. Common Specifications of Rebar Tie Wire
Rebar tie wire is typically available in different specifications based on the material, tensile strength, and coating (if any). The key factors to consider include:
-
Wire Gauge (Thickness):
The wire gauge refers to the thickness of the wire. Generally, rebar tie wire ranges from 0.6 mm to 1.5 mm in diameter, with the most common sizes being 0.8 mm, 1.0 mm, and 1.2 mm. The gauge of the wire affects its flexibility, strength, and ease of use.- 0.6 mm to 0.8 mm: Typically used for smaller projects or lighter rebar tying where less strength is required.
- 1.0 mm to 1.2 mm: Commonly used in most standard construction projects for medium-strength requirements.
- 1.4 mm to 1.5 mm: Suitable for heavy-duty construction projects with higher strength requirements, such as large buildings, bridges, and other high-load structures.
-
Tensile Strength:
The tensile strength of rebar tie wire refers to the force the wire can withstand before breaking. It’s essential to choose a wire with the right tensile strength to secure the rebar effectively and ensure structural stability. Typically, tie wire has a tensile strength of 450 to 800 MPa. The higher the tensile strength, the more force the wire can handle, which is particularly important in projects that require additional stability.
2. Length of Rebar Tie Wire
The length of rebar tie wire is another important consideration, as it impacts both cost and ease of handling. Rebar tie wire typically comes in the following forms:
-
Coiled Wire:
The most common form of rebar tie wire is coiled wire. This allows for easy dispensing and cutting to the desired length during construction. Coiled wire typically comes in lengths of 50 meters (164 feet), 100 meters (328 feet), or 200 meters (656 feet) per coil, but other lengths are also available based on the supplier and project needs. -
Pre-cut Wire (Straightened & Cut):
For convenience and faster installation, pre-cut wire may be provided in lengths of 300 mm to 600 mm (12 to 24 inches), depending on the project requirements. This eliminates the need to manually cut and bend the wire on-site, saving time during construction.
3. Common Sizes and Their Applications
Rebar tie wire is available in several common sizes, each suited for different types of construction projects. Below is a general guide to the most common sizes and their typical uses:
Wire Diameter (mm) | Typical Application | Advantages |
---|---|---|
0.6 mm to 0.8 mm | Small residential projects, light reinforcement | Flexible, easy to work with, cost-effective |
1.0 mm to 1.2 mm | Medium to large construction projects, commercial buildings | Standard use, versatile, balanced strength |
1.4 mm to 1.5 mm | Heavy-duty projects, high-strength requirements | High tensile strength, ideal for large structures like bridges and high-rise buildings |
1.2 mm (Galvanized) | Use in outdoor and corrosive environments (e.g., coastal areas) | Corrosion-resistant, durable in harsh conditions |
4. Wire Coating and Treatment
The wire coating plays an essential role in determining the wire’s durability and resistance to environmental factors. While plain steel is susceptible to rust and corrosion, galvanized steel and stainless steel coatings offer much higher resistance to moisture and chemicals.
-
Galvanized Tie Wire:
This type of wire is coated with a layer of zinc, providing corrosion resistance and making it ideal for use in outdoor or humid environments. Typically, galvanized wire is available in 0.8 mm to 1.2 mm diameter and is a popular choice for most construction projects. -
Stainless Steel Tie Wire:
Stainless steel wire is ideal for extremely corrosive environments, such as coastal areas or chemical plants. It is highly durable and resistant to rust, making it suitable for long-term applications where durability is critical.
5. Choosing the Right Size for Your Project
Selecting the correct wire size depends on several factors, such as the project scale, rebar size, and environmental conditions. Here are some general guidelines:
- Small Projects or Indoor Use: For small-scale construction or indoor applications where corrosion resistance is less of a concern, a 0.8 mm to 1.0 mm plain steel tie wire will suffice.
- Standard Commercial Projects: For general construction needs, such as residential buildings or mid-sized commercial projects, 1.0 mm to 1.2 mm galvanized tie wire is a common choice. It provides a good balance between strength, flexibility, and corrosion resistance.
- Heavy-Duty or Outdoor Projects: If your project involves heavy-duty construction or is located in a corrosive environment (e.g., coastal regions), a 1.2 mm to 1.5 mm galvanized or stainless steel tie wire is ideal.
Selecting the right rebar tie wire size and specification is essential to ensure the durability, stability, and cost-effectiveness of your construction project. Consider factors such as wire gauge, tensile strength, and environmental conditions when choosing the right wire for your needs. By understanding the specifications and sizes of rebar tie wire, you can ensure that your construction projects are completed safely and efficiently, while also optimizing costs and performance.
How does Environmental Factors Affect Rebar Tie Wire?
The choice of rebar tie wire material and specification is significantly influenced by environmental factors, as these conditions can directly affect the wire’s performance, durability, and longevity. Whether you’re working on a construction site in a coastal region, a humid climate, or a high-temperature environment, it’s essential to consider how these factors can impact the tie wire. In this section, we will explore the key environmental conditions that affect rebar tie wire, including moisture, temperature, corrosion, and exposure to chemicals.
1. Moisture and Humidity
Moisture is one of the most significant factors affecting the longevity and strength of rebar tie wire. Environments with high humidity, frequent rainfall, or direct exposure to water can cause certain types of tie wire to corrode or degrade more quickly. The effects of moisture on rebar tie wire depend on the material:
-
Plain Steel Tie Wire:
Plain steel (non-galvanized) tie wire is highly susceptible to rust and corrosion when exposed to moisture. If the wire is used in environments where water is present (e.g., coastal areas, wet climates, or construction sites prone to rain), it will degrade much faster than galvanized or stainless steel wire. -
Galvanized Tie Wire:
Galvanized tie wire, coated with a protective layer of zinc, is far more resistant to moisture and corrosion. The zinc layer helps prevent rust from forming on the steel, making it an ideal choice for construction projects in humid environments, such as coastal areas, basements, or areas with heavy rainfall. -
Stainless Steel Tie Wire:
Stainless steel tie wire is the best choice for highly corrosive environments, such as areas with extreme humidity or saltwater exposure. It is highly resistant to rust and corrosion and performs well in environments prone to high moisture levels, such as marine construction projects, chemical plants, and sewage systems.
2. Corrosive Environments
Construction sites near chemicals, saltwater, or other corrosive substances require rebar tie wire that can withstand aggressive conditions. Materials such as galvanized or stainless steel are preferred in such environments due to their enhanced corrosion resistance.
-
Saltwater and Coastal Environments:
Coastal construction projects face the challenge of salt exposure, which can accelerate the corrosion of plain steel tie wire. Even galvanized wire may degrade over time in saltwater environments, although the zinc coating provides some protection. Stainless steel, however, offers superior resistance to corrosion in saltwater, making it the best choice for marine environments. -
Chemical Exposure:
Chemical plants, wastewater treatment facilities, and other industrial sites often use chemicals that can degrade metal materials. In these cases, stainless steel tie wire is often required to withstand exposure to acids, alkalis, or other corrosive substances. Stainless steel provides excellent resistance against chemical corrosion, ensuring long-term durability and reliability.
3. Temperature Extremes
Temperature fluctuations, including extremely high or low temperatures, can also affect the performance of rebar tie wire. Different materials react differently to temperature changes, so choosing the right wire for the climate and project conditions is crucial.
-
High Temperatures:
In hot environments or construction projects where high temperatures are present (e.g., desert regions, steel mills), rebar tie wire made from plain steel or galvanized wire can experience reduced strength or deformation. High temperatures can cause the wire to lose flexibility, making it more difficult to work with. Stainless steel wire, due to its higher melting point and thermal stability, is more suitable for high-temperature environments, maintaining its strength and flexibility even under extreme heat. -
Low Temperatures:
In cold climates, rebar tie wire can become brittle and prone to breakage if not made from the appropriate material. Steel wire can become more rigid in low temperatures, making it harder to twist and tie securely. Stainless steel is more resistant to cold-induced brittleness and maintains its flexibility in freezing temperatures, which is especially important for construction in areas with harsh winters or extremely low temperatures.
4. Exposure to UV Light and Outdoor Conditions
When rebar tie wire is used in outdoor construction, it is often exposed to ultraviolet (UV) light, which can degrade certain materials over time. UV radiation can break down the zinc coating on galvanized wire, reducing its corrosion resistance and making it more prone to rust.
-
Galvanized Tie Wire:
While galvanized wire provides excellent corrosion resistance initially, prolonged exposure to UV light can cause the zinc layer to deteriorate. In areas with high levels of UV radiation, such as desert environments, it is important to regularly inspect the wire for signs of wear. For extended outdoor use, stainless steel wire may be a better choice as it is not susceptible to UV degradation and retains its corrosion resistance longer. -
Plain Steel Tie Wire:
Plain steel wire, being uncoated, is susceptible to rusting and degradation when exposed to UV light and outdoor conditions. This type of wire is typically not recommended for projects that require prolonged outdoor exposure unless the wire is shielded or used in environments where UV radiation is minimal.
5. Soil Conditions
In construction projects where rebar is embedded in the soil, such as foundations, underground parking garages, or tunnels, the type of soil can impact the choice of rebar tie wire. Soil containing high levels of moisture, salt, or other corrosive elements can accelerate corrosion, especially if the wire is not protected.
-
Galvanized and Stainless Steel Tie Wire:
Both galvanized and stainless steel tie wires offer superior protection against corrosion in soil, especially in areas with saline or chemically aggressive soil. These wires are commonly used in foundation work and other underground construction where exposure to soil moisture and chemicals is inevitable. -
Plain Steel Tie Wire:
Plain steel tie wire should be avoided for projects where it will be exposed to soil for prolonged periods, as it will corrode much faster in these conditions. If plain steel wire is used, it should be properly coated or treated to prevent rust.
6. Wind and Other Mechanical Factors
In regions with high winds or construction sites where mechanical wear and tear are concerns (such as building projects near highways or industrial areas), the tie wire must be strong and resilient.
- High-Strength Steel Tie Wire:
In environments where mechanical stress or wind is a factor, high-strength steel tie wire (or higher-gauge wire) is more appropriate. The tensile strength of the wire must be high enough to resist the forces placed upon it, ensuring secure rebar tying even in windy or harsh mechanical environments.
Environmental factors play a significant role in determining the type of rebar tie wire that should be used for a particular project. Moisture, humidity, exposure to corrosive substances, extreme temperatures, and soil conditions all influence the durability and performance of tie wire. When selecting rebar tie wire, it is essential to consider these environmental factors and choose the material that best suits the specific conditions of your construction project. Galvanized wire is a good option for many projects, while stainless steel is ideal for the most corrosive or extreme conditions. By taking the environment into account, you can ensure the longevity and reliability of your rebar tie wire, ultimately contributing to the safety and durability of your construction.
How to Assess the Quality and Performance of Tie Wire?
Selecting high-quality rebar tie wire is essential to ensure the safety, stability, and durability of a construction project. The quality and performance of tie wire are influenced by several factors, including its tensile strength, flexibility, durability, coating, and resistance to environmental conditions. In this section, we will discuss key aspects to consider when assessing the quality and performance of rebar tie wire, ensuring that you choose the most suitable option for your specific needs.
1. Tensile Strength of Tie Wire
Tensile strength refers to the amount of force a material can withstand without breaking. For rebar tie wire, high tensile strength is crucial because it ensures that the wire can securely hold the rebar in place without snapping under pressure. A wire with too low tensile strength may fail during installation, compromising the structural integrity of the reinforcement.
- What to Look For:
- Minimum Tensile Strength: The typical tensile strength for rebar tie wire ranges from 450 MPa to 800 MPa. For most construction projects, tie wire with a tensile strength between 500 MPa and 700 MPa is sufficient.
- Certification or Testing: High-quality tie wire should be tested and certified according to national or international standards (e.g., ASTM, EN, or ISO). Check for any quality certifications or lab reports to verify the wire’s tensile strength.
- Material Impact: Galvanized or stainless steel tie wire may have different tensile strength levels compared to plain steel. Always verify whether the wire type meets the necessary strength requirements for your specific application.
2. Flexibility and Workability
While strength is important, flexibility is equally critical for tie wire. The wire must be easy to bend, twist, and tie securely around the rebar. Tie wire that is too rigid can make installation difficult, leading to inefficient work processes and potential safety hazards.
- What to Look For:
- Ease of Handling: High-quality tie wire should be flexible enough for easy handling without excessive force. It should allow for tight twists and secure knots around the rebar.
- Wire Gauge: Generally, thinner wire (e.g., 0.8 mm to 1.0 mm) is more flexible and easier to work with, while thicker wire (e.g., 1.2 mm to 1.5 mm) is stronger but may be slightly more rigid. Choose a wire gauge that balances flexibility and strength based on the project requirements.
- Coating Consideration: Galvanized and stainless steel wires tend to have different levels of flexibility compared to plain steel. Galvanized wires may be slightly less flexible due to the coating, while stainless steel wire provides a balance between flexibility and strength.
3. Durability and Resistance to Wear
Durability refers to the wire’s ability to withstand physical wear and environmental factors over time. Tie wire used in construction needs to perform reliably throughout the duration of the project, whether it’s being exposed to harsh weather conditions or handled frequently during installation.
- What to Look For:
- Coating Integrity: For galvanized wire, check for a uniform coating of zinc. A wire with an uneven or damaged coating may lose its corrosion resistance, reducing its overall durability. Stainless steel wire should show no signs of corrosion or tarnishing.
- Resistance to Abrasions: The wire should maintain its form without significant wear or fraying during installation. Poor-quality wire may show signs of breakage or abrasions when subjected to bending and twisting.
- Longevity in Harsh Environments: In environments with high exposure to chemicals, moisture, or temperature fluctuations, stainless steel tie wire offers superior durability compared to galvanized or plain steel options.
4. Corrosion Resistance
Corrosion is one of the most common issues affecting the performance of rebar tie wire. The wire is often exposed to moisture, chemicals, and other corrosive elements during and after installation, which can weaken it over time. High-quality tie wire should provide sufficient protection against corrosion to ensure the long-term integrity of the structure.
- What to Look For:
- Galvanized Coating Quality: In galvanized wire, the zinc coating should be thick and evenly distributed to provide effective corrosion resistance. Thin or damaged coatings can allow corrosion to develop faster.
- Stainless Steel Resistance: Stainless steel wire is naturally resistant to corrosion, making it ideal for use in coastal or chemical environments where moisture and corrosive elements are prevalent.
- Resistance to Environmental Stress: High-quality tie wire should withstand various environmental stress factors, including exposure to moisture, humidity, UV radiation, and chemicals. This is especially important for projects located in areas with high salt content or corrosive industrial environments.
5. Consistency in Wire Diameter and Quality Control
Inconsistent wire diameter can lead to difficulties in tying the rebar and may affect the overall strength of the structure. High-quality tie wire should have a consistent diameter and uniform properties throughout the entire length of the wire. Inconsistent wire gauge can result in weak spots, where the wire may break under stress.
- What to Look For:
- Wire Diameter: Check for consistency in wire gauge along the entire length of the wire. A good quality tie wire will have a uniform thickness, allowing for consistent performance.
- Surface Smoothness: The wire should be smooth without any sharp edges, burrs, or deformations. Rough surfaces can make handling difficult and increase the risk of injury during installation.
6. Compliance with Industry Standards
To ensure the wire meets the required performance criteria, it is important to check that it complies with recognized industry standards. Quality tie wire manufacturers often provide certifications that verify the wire’s compliance with national or international standards.
- What to Look For:
- Certifications: Look for certifications such as ISO 9001, ASTM A82, or EN 10270 that confirm the wire’s adherence to quality standards. These certifications ensure that the wire meets specific strength, flexibility, and corrosion resistance criteria.
- Manufacturer Reputation: Choose suppliers with a strong reputation for providing high-quality materials. Established manufacturers will often have quality control processes in place to ensure consistency and reliability.
7. Packaging and Delivery
The way tie wire is packaged and delivered can also impact its quality and ease of use. High-quality wire should arrive in optimal condition, free from rust, tangles, or other forms of damage.
- What to Look For:
- Proper Packaging: Tie wire should be packaged in a way that prevents tangling, damage, or contamination. Coiled wire should be neatly wound and secured to prevent deformation.
- Storage Conditions: Ensure that the tie wire is stored in dry, climate-controlled environments to prevent moisture exposure that could lead to rust or corrosion before use.
Assessing the quality and performance of rebar tie wire is crucial for ensuring that your construction projects are completed safely, efficiently, and with lasting durability. Key factors to consider include tensile strength, flexibility, corrosion resistance, durability, and compliance with industry standards. By carefully evaluating these aspects, you can select tie wire that will perform reliably in your specific construction environment, ultimately contributing to the overall success of the project.
How to Choose the Right Tie Wire Based on Project Needs?
Selecting the right rebar tie wire is critical for ensuring the durability, safety, and efficiency of your construction project. The type of tie wire you choose should be based on a variety of factors, such as the project’s scale, environmental conditions, rebar size, and overall performance requirements. Here, we break down the process of choosing the right tie wire for your specific project needs.
1. Consider the Type of Project
Different construction projects have different requirements for rebar tie wire, depending on the scale, location, and materials involved.
-
Residential and Small-Scale Projects:
For smaller, residential projects, such as home foundations or small commercial buildings, plain steel tie wire (non-galvanized) is usually sufficient. It’s cost-effective, easy to work with, and provides the strength needed for these types of structures. If the project is located in an area with low exposure to moisture or chemicals, plain steel wire is often a suitable choice. -
Commercial and Industrial Projects:
For larger commercial or industrial projects, such as office buildings, shopping malls, or warehouses, galvanized steel tie wire is often the best option. Galvanized wire provides better corrosion resistance, which is essential for larger structures exposed to moisture and external elements during construction. It also offers long-term durability and ensures the safety of the rebar over time. -
Heavy-Duty and Large-Scale Infrastructure:
For projects involving heavy-duty applications, such as bridges, highways, tunnels, or dams, stainless steel tie wire is highly recommended. This wire offers superior tensile strength, corrosion resistance, and long-term performance under extreme conditions. Stainless steel wire is particularly well-suited for environments with high moisture, exposure to saltwater, or chemical agents.
2. Assess Environmental Conditions
The environmental conditions at your construction site will significantly influence the type of tie wire you should choose. Various factors, such as humidity, temperature, exposure to chemicals, and moisture, can impact the performance of the wire.
-
Humid or Coastal Areas:
In regions with high humidity, such as coastal areas or areas with significant rainfall, galvanized or stainless steel tie wire should be prioritized. Galvanized wire is coated with a protective layer of zinc, which helps prevent corrosion in moisture-rich environments. Stainless steel, however, offers the highest corrosion resistance and is ideal for marine environments or areas with salt exposure. -
Chemical Exposure:
For construction projects in chemical plants, factories, or wastewater treatment facilities, stainless steel tie wire is the preferred choice. Stainless steel offers exceptional resistance to chemicals and acids, ensuring the tie wire remains strong and functional in harsh environments where other materials might corrode quickly. -
Extreme Temperatures:
For projects in regions with extremely high or low temperatures, such as deserts or frozen climates, stainless steel or high-strength galvanized wire is recommended. These materials are better able to withstand temperature extremes without becoming brittle or losing tensile strength, ensuring reliable performance under stress.
3. Evaluate the Rebar Size and Load Requirements
The size and load capacity of the rebar being used will also influence the choice of tie wire. Larger and heavier rebar typically requires stronger tie wire with a higher tensile strength.
-
Smaller Rebar (Light Loads):
For smaller rebar or reinforcement with lower load-bearing requirements, 0.6 mm to 1.0 mm diameter tie wire is typically sufficient. This wire is flexible enough to handle the lighter rebar, while still offering the necessary strength to hold the reinforcement securely in place. -
Larger Rebar (Heavy Loads):
For larger rebar (e.g., in foundation work, large commercial buildings, or bridges), you will need 1.2 mm to 1.5 mm diameter wire. Thicker wire offers higher tensile strength and ensures the rebar stays in place under heavy loads. Galvanized or stainless steel wires are often preferred for these projects due to their increased strength and resistance to environmental factors.
4. Determine the Corrosion Resistance Required
The level of corrosion resistance needed depends on the environment and the expected exposure to moisture, chemicals, and other corrosive agents.
-
Moderate Corrosion Resistance:
For areas with moderate moisture, such as residential foundations or commercial buildings in temperate climates, galvanized tie wire is an excellent choice. The zinc coating on galvanized wire provides a good balance of corrosion resistance and strength, making it suitable for environments with occasional moisture exposure. -
High Corrosion Resistance:
In areas with high corrosion risk, such as coastal or chemical environments, stainless steel tie wire is the best option. Stainless steel has exceptional resistance to corrosion, rust, and environmental degradation, ensuring long-term reliability even in the harshest conditions. It is particularly useful in marine, coastal, or industrial construction where exposure to saltwater or chemicals is inevitable.
5. Budget Considerations
Cost is an important factor to consider when choosing the right tie wire, as different types of wire come at varying price points. While higher-performance options such as stainless steel offer superior corrosion resistance and strength, they can be significantly more expensive than plain steel or galvanized wire.
-
Cost-Effective Projects:
For budget-conscious projects, plain steel tie wire is the most affordable option and is ideal for indoor applications or projects in areas with low moisture and environmental stress. While it lacks the corrosion protection of galvanized or stainless steel, it provides sufficient strength for most residential and light commercial projects. -
Long-Term Investment:
If the project involves outdoor construction, exposure to moisture, or harsh environmental conditions, investing in galvanized or stainless steel tie wire can save money in the long term by reducing the need for repairs or replacements. These wires are more durable, offering better protection against rust and degradation over time.
6. Workability and Ease of Use
The ease of handling and working with tie wire is an important consideration, especially for large-scale projects where the wire needs to be handled frequently during rebar installation.
-
Flexibility and Bending:
Tie wire should be flexible enough to bend, twist, and secure the rebar tightly without breaking. Thinner wires (0.6 mm to 1.0 mm) are generally easier to work with and can be bent into tight knots quickly. However, for heavier or larger rebar, stronger wires (1.2 mm to 1.5 mm) are necessary to ensure secure holding power. -
Coiling and Pre-Cutting:
Coiled tie wire is the most common form and allows for flexible use. Some suppliers also offer pre-cut tie wire, which can speed up the tying process and reduce the need for on-site cutting. If time efficiency is a priority, pre-cut wire may be the better choice.
7. Durability and Long-Term Performance
Finally, consider the long-term performance of the wire. If the structure will be exposed to harsh weather or environmental stress over an extended period, choose a tie wire that can withstand wear and tear, corrosion, and fatigue.
- Long-Term Durability:
For construction projects that require long-lasting reinforcement, galvanized or stainless steel tie wire is highly recommended. These materials offer superior durability, making them suitable for heavy-duty and large-scale infrastructure projects where structural integrity is paramount.
Choosing the right rebar tie wire depends on a variety of factors, including the type of project, environmental conditions, rebar size, and budget. For small-scale, indoor projects, plain steel tie wire is often sufficient, while larger commercial or industrial projects may benefit from galvanized or stainless steel tie wire due to their superior corrosion resistance and strength. By considering these factors carefully, you can select the best tie wire to meet your project’s specific needs, ensuring the safety and longevity of the structure.
Product Recommendations and Supplier Tips for Rebar Tie Wire
When selecting rebar tie wire, it’s important to choose products that not only meet your project requirements but also offer durability, cost-effectiveness, and reliability. As a supplier or contractor, understanding the different types of tie wire available and the unique benefits each offers can help ensure you make the right choice for your construction needs. Below are product recommendations for different use cases, as well as valuable supplier tips to help you select high-quality rebar tie wire and manage your procurement process effectively.
1. Product Recommendations
1.1 Plain Steel Tie Wire (Non-Galvanized)
Best For: Small-scale, residential, and indoor projects with minimal exposure to moisture and corrosive elements.
- Description: Plain steel tie wire is the most basic and cost-effective option. It is made from untreated carbon steel, making it more prone to rust and corrosion. However, it is strong and flexible, which makes it suitable for general reinforcement applications in dry and sheltered environments.
- Advantages:
- Cost-effective for smaller projects
- Flexible and easy to work with
- Good for low-moisture environments
- Limitations:
- Prone to rust and corrosion over time
- Not suitable for coastal or chemical exposure
- Recommended For:
- Residential construction (foundations, walls)
- Small commercial buildings or interior structures
- Temporary reinforcement projects
1.2 Galvanized Steel Tie Wire
Best For: Commercial projects and environments with moderate exposure to moisture or external elements, such as office buildings, shopping centers, or residential foundations in humid climates.
- Description: Galvanized tie wire is coated with a layer of zinc to protect against corrosion, making it more durable than plain steel wire. This wire type is ideal for environments that may experience moisture, including areas with occasional rainfall or humidity.
- Advantages:
- Excellent corrosion resistance
- Increased durability compared to plain steel
- Suitable for moderate outdoor exposure
- Limitations:
- Slightly more expensive than plain steel
- Galvanized coating can wear off over time in highly corrosive environments
- Recommended For:
- Commercial construction projects (office buildings, retail stores)
- Foundations in regions with moderate rainfall or humidity
- Projects with medium-term exposure to outdoor elements
1.3 Stainless Steel Tie Wire
Best For: High-performance applications, especially in corrosive environments such as coastal areas, chemical plants, and marine construction.
- Description: Stainless steel tie wire is known for its exceptional resistance to corrosion, rust, and environmental wear. While it is more expensive than both plain steel and galvanized wire, its strength and longevity make it ideal for high-stakes construction projects or projects exposed to severe environmental conditions.
- Advantages:
- Superior corrosion resistance, even in marine or chemical environments
- Extremely strong and durable, ideal for high-load applications
- Suitable for long-term projects with exposure to saltwater, chemicals, or harsh weather
- Limitations:
- Higher cost compared to plain or galvanized wire
- Slightly less flexible than galvanized wire, though still workable
- Recommended For:
- Coastal or marine construction projects (e.g., piers, seawalls)
- Chemical plants, sewage systems, or areas exposed to industrial pollutants
- Large-scale infrastructure projects requiring maximum durability
1.4 High-Strength Steel Tie Wire
Best For: Heavy-duty applications where the tie wire needs to endure extreme loads and high mechanical stress, such as in bridges or heavy industrial buildings.
- Description: High-strength steel tie wire is made from alloyed steel designed to withstand higher tensile loads. It’s commonly used for large-scale projects where rebar requires extra strength to handle significant pressure and load.
- Advantages:
- High tensile strength for heavy-duty applications
- Durable under extreme mechanical stress
- Reliable for infrastructure projects subject to heavy loads
- Limitations:
- More difficult to work with due to its rigidity
- Higher cost than regular steel wire
- Recommended For:
- Bridges, tunnels, and other infrastructure requiring extra reinforcement
- Industrial plants with heavy machinery or large foundations
- High-load bearing projects
2. Supplier Tips for Rebar Tie Wire Procurement
As a supplier, choosing the right tie wire involves not just selecting the right product but also ensuring reliable sourcing, quality control, and timely delivery. Here are key supplier tips to help you manage your procurement process efficiently:
2.1 Source from Reputable Manufacturers
- Quality Certifications: Always work with manufacturers that hold relevant quality certifications, such as ISO 9001 (Quality Management) or ISO 14001 (Environmental Management). These certifications ensure that the tie wire meets international standards for strength, flexibility, and corrosion resistance.
- Factory Audits: Consider performing regular audits or quality checks at the manufacturer’s facilities to verify the consistency of the wire’s quality.
- Material Traceability: Choose suppliers who can provide clear documentation of the material’s origin and quality testing results. This helps ensure that the wire meets performance requirements and provides transparency in case of any issues.
2.2 Know Your Local Standards and Regulations
- Compliance with Local Codes: Different countries or regions may have specific standards or building codes for construction materials, including tie wire. Make sure the tie wire you select meets the relevant local regulations and standards.
- Testing Requirements: Some construction projects, particularly larger commercial or industrial ones, may require materials to pass specific mechanical or environmental tests. Ensure that your tie wire complies with these standards to avoid costly delays or rejections.
2.3 Evaluate the Wire’s Coating
- Galvanized Coating Thickness: When sourcing galvanized wire, pay attention to the thickness of the zinc coating. Thicker coatings provide better corrosion resistance, especially in environments prone to moisture or industrial pollutants.
- Stainless Steel Quality: If you’re sourcing stainless steel wire, ensure that the wire is made from 304 or 316 grade stainless steel, which offers excellent resistance to corrosion and environmental factors.
2.4 Focus on Consistency and Packaging
- Uniform Diameter: Consistent wire diameter is essential to ensure uniform performance. Check that the tie wire you source maintains consistent gauge throughout the roll or spool, as inconsistencies can affect its workability and strength.
- Packaging for Safety: Tie wire should be packaged securely to prevent tangling or damage. Coiled wire should be tightly wound and free from deformities. If the wire is pre-cut, ensure that it is packaged in a way that prevents rusting or contamination.
2.5 Assess Delivery and Lead Times
- On-Time Delivery: Ensure that your supplier offers reliable delivery schedules. Delays in wire delivery can hold up the entire construction project, leading to delays and increased costs.
- Bulk Orders: For large projects, consider negotiating bulk order discounts. Suppliers often offer better pricing for large-volume orders, which can help reduce overall material costs for the project.
2.6 Consider Pricing and Budget
- Cost-Effectiveness: While stainless steel offers the best performance, it is also the most expensive. For projects that don’t require the highest level of corrosion resistance or durability, galvanized or plain steel wire may provide a more cost-effective solution.
- Long-Term Value: While plain steel wire may be cheaper initially, galvanized or stainless steel wires provide greater longevity and reduced maintenance costs over time, making them better investments for high-risk environments.
2.7 Offer Custom Solutions for Specific Needs
- Wire Length and Packaging Options: Offer custom wire lengths, pre-cut wire, or specific coil sizes to meet the needs of your clients. Some projects may require shorter wire lengths for quicker installation or custom packaging to fit the project scale.
- Custom Coatings: For specialized projects, offer custom coatings or treated wire to meet specific environmental or mechanical requirements.
Choosing the right tie wire is essential to the success of a construction project, impacting both short-term installation and long-term structural integrity. Whether you need plain steel, galvanized, stainless steel, or high-strength wire, understanding the specific requirements of your project and sourcing from reputable suppliers will ensure you select the best tie wire for your needs. By considering environmental conditions, rebar size, project scale, and budget, you can make a well-informed decision that supports the durability and safety of the entire structure.
When selecting rebar tie wire, understanding the material, specifications, and environmental conditions is crucial. Hot-dipped galvanized and stainless steel tie wires are ideal for corrosive environments, while regular steel tie wire works well for most general construction projects. By considering your construction needs and budget, you can choose the most suitable tie wire, ensuring both construction efficiency and safety. We hope this article provides useful purchasing advice to help you make better decisions when sourcing rebar tie wire.